Introduction to Chamber Furnaces
When it comes to heat treatment processes, having the right equipment is crucial. Chamber furnaces are at the heart of this industry, providing precise control over temperature and atmosphere for various materials. But not all chamber furnaces are created equal. As businesses look to optimize their operations, custom solutions have become more than just a trend; they’re a necessity. Tailored chamber furnaces ensure that unique specifications are met, enhancing efficiency and effectiveness in heat treatment applications.
Imagine a furnace designed specifically with your needs in mind—a piece of equipment that not only handles materials seamlessly but also integrates into your production workflow effortlessly. This blog delves deep into the world of custom chamber furnaces, exploring their types, benefits, and what factors you should consider when selecting one for your facility. Get ready to discover how investing in customized solutions can elevate your heat treatment results like never before!
Different Types of Chamber Furnaces
Chamber furnaces come in various types, each designed for specific applications. The most common categories are electric and gas chamber furnaces. Electric models offer precise temperature control and energy efficiency, making them ideal for intricate heat treatment processes.
Gas-powered chamber furnaces, on the other hand, provide faster heating times and higher temperatures. They work well in industrial settings where large volumes of materials need processing quickly.
Within these categories, you’ll find options such as box-style or vertical chambers. Box-type furnaces are versatile and suitable for a range of materials, while vertical designs maximize space utilization.
Specialized versions include vacuum chamber furnaces that eliminate oxidation during heat treatment. This feature is crucial for sensitive materials.
Each type serves unique needs within industries like aerospace, automotive, and manufacturing. Understanding the different options helps businesses choose the right furnace to meet their specific requirements efficiently.
Benefits of Customized Chamber Furnaces
Customized chamber furnaces offer numerous advantages that can significantly enhance heat treatment processes. One of the primary benefits is precision. These furnaces are designed to meet specific requirements, ensuring consistent and uniform heating throughout.
Another key advantage is flexibility. Custom solutions allow for adjustments in temperature ranges, cycle times, and atmosphere control tailored to particular materials or products. This adaptability can lead to improved material properties and performance.
Energy efficiency is also a major plus. Tailored designs can minimize energy consumption by optimizing thermal dynamics within the furnace space. Lower operational costs contribute positively to your bottom line over time.
Moreover, customized chamber furnaces often incorporate advanced technology features such as automated controls and monitoring systems. This not only simplifies operation but also enhances safety measures during high-temperature processing.
Investing in a custom solution fosters innovation in manufacturing processes while meeting industry standards with greater ease.
Factors to Consider When Choosing a Custom Chamber Furnace
Selecting the right custom chamber furnace requires careful consideration of several key factors. First, think about the specific heat treatment processes you will be performing. Each application has different temperature and atmosphere requirements that can influence your choice.
Next, consider the material compatibility of the furnace. Different materials react uniquely to heat, so ensure your furnace can handle them without compromising performance or safety.
Size matters too; evaluate how much space you have available in your facility and how large a unit you’ll need for optimal efficiency.
Energy consumption is another important aspect to weigh. An energy-efficient model not only cuts costs but also contributes positively to environmental efforts.
Don’t overlook technical support and maintenance services offered by manufacturers. Reliable assistance ensures longevity and functionality over time, which is crucial for any production environment.
Case Studies: Real-Life Examples of Effective Custom Chamber Furnaces
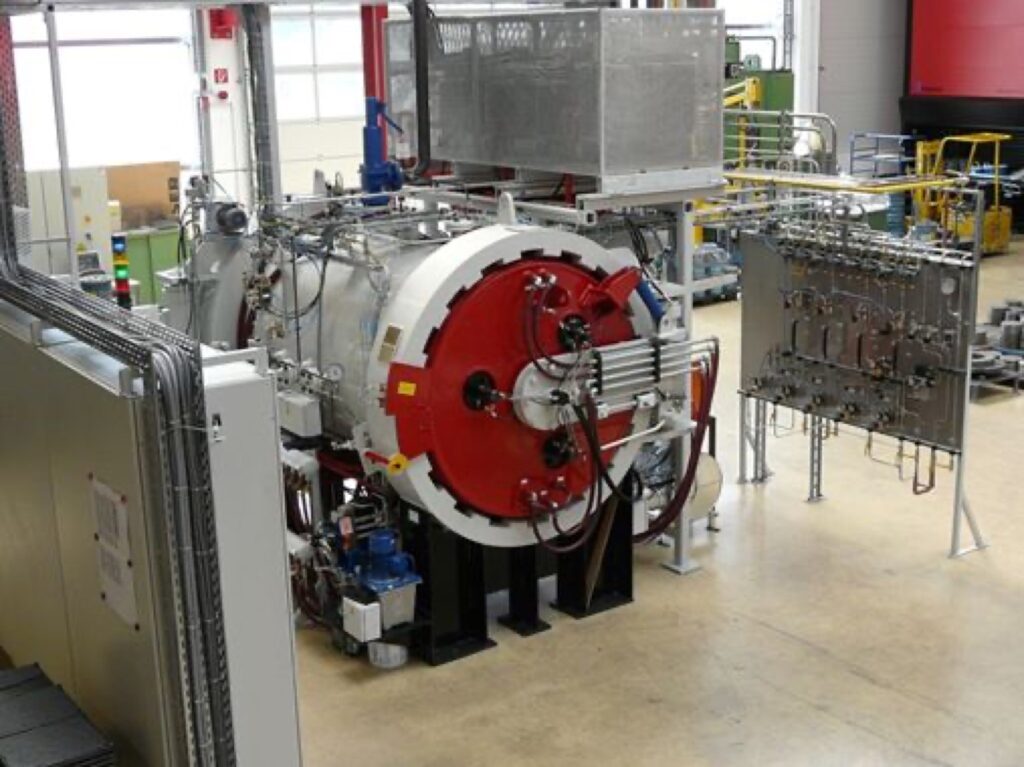
One notable case involved a large aerospace manufacturer facing challenges with uniform heat treatment of titanium components. They implemented a custom chamber furnace designed specifically for their unique production needs. The results were astonishing, achieving precise temperature control and reduced cycle times.
In another instance, a medical device company required stringent sterilization processes for various metal parts. A tailored chamber furnace was developed to accommodate different sizes and materials while maintaining consistent heating profiles. This led to significant improvements in product quality.
A third example highlights an automotive parts supplier who needed to enhance the efficiency of their carburizing process. By investing in a specialized chamber furnace, they experienced faster processing rates and minimized energy consumption—important factors in today’s competitive market.
These real-life applications illustrate how customized solutions can effectively address specific industry requirements and elevate operational performance seamlessly.
The Importance of Regular Maintenance and Upkeep
Regular maintenance of chamber furnaces is essential for optimal performance. A well-maintained furnace operates efficiently, ensuring consistent temperature control and uniform heat distribution.
Neglecting upkeep can lead to unexpected breakdowns. These interruptions can be costly, both in terms of repairs and lost productivity. Regular check-ups help identify potential issues before they escalate.
Cleaning is another crucial aspect. Dust and debris accumulation can affect the heating elements and insulation, leading to reduced efficiency. Routine inspections keep these components in top shape.
Moreover, regular maintenance extends the lifespan of your equipment. By addressing wear and tear promptly, you enhance durability and reliability over time.
Keeping a detailed maintenance log helps track service history. This documentation proves invaluable when troubleshooting or upgrading systems down the line. Prioritizing upkeep fosters an environment where heat treatment processes thrive without disruption.
Conclusion: Investing in a Custom Chamber Furnace for Optimal Heat Treatment Results
When it comes to achieving optimal heat treatment results, investing in a custom chamber furnace is a strategic choice. These systems provide tailored solutions that enhance performance and efficiency for various applications.
Customizing your chamber furnace allows you to meet specific requirements that standard models may not satisfy. You’ll benefit from adjustments in size, temperature range, and atmosphere control, all of which can significantly impact your processes.
Moreover, the advantages extend beyond immediate functionality. A well-designed custom chamber furnace can lead to longer equipment life and reduced operational costs over time. This kind of investment pays off as you see improved quality in your products.
As industries continue to evolve, staying ahead means having the right equipment designed specifically for your needs. By choosing a custom solution, you’re setting up your operation for success now and into the future.
Consider making this vital investment today—it’s an essential step toward achieving superior heat treatment outcomes that will propel your business forward.