Introduction to Tube Furnaces
When it comes to precision heating, tube furnaces stand out as a versatile and efficient solution. These specialized systems play a crucial role in various industrial applications, providing controlled environments for processes like material testing, sintering, and even semiconductor manufacturing. But what makes custom tube furnaces truly remarkable is their ability to be tailored to specific needs, delivering unparalleled performance.
Imagine having the power to dictate every aspect of your heating process—from temperature accuracy to atmosphere control—ensuring optimal results every time. With advancements in technology and engineering, custom tube furnaces are becoming increasingly accessible across industries. Whether you’re in research or production, understanding these innovative tools can transform your operations significantly.
Join us as we delve into the world of custom tube furnaces—a place where precision meets adaptability. You’ll discover different types available on the market today, explore their numerous benefits, and learn how they can fit into your unique application needs. Get ready for an enlightening journey through the realm of precision heating solutions!
Types of Tube Furnaces
Tube furnaces come in various types, each designed for specific heating needs. One common type is the horizontal tube furnace, which offers consistent heat distribution along its length. This design is ideal for processes that require uniform temperature control.
Another type is the vertical tube furnace. It’s perfect for applications where space is limited, allowing efficient use of laboratory or industrial areas.
There are also split-tube furnaces, providing versatility with a removable section that allows easy access to samples while maintaining precise thermal conditions during experiments.
For high-temperature applications, you might consider a quartz tube furnace. These units can withstand extreme temperatures and offer excellent chemical resistance.
Each variant caters to different industries and processes, ensuring users find the right fit for their unique heating requirements.
Benefits of Using a Custom Tube Furnace
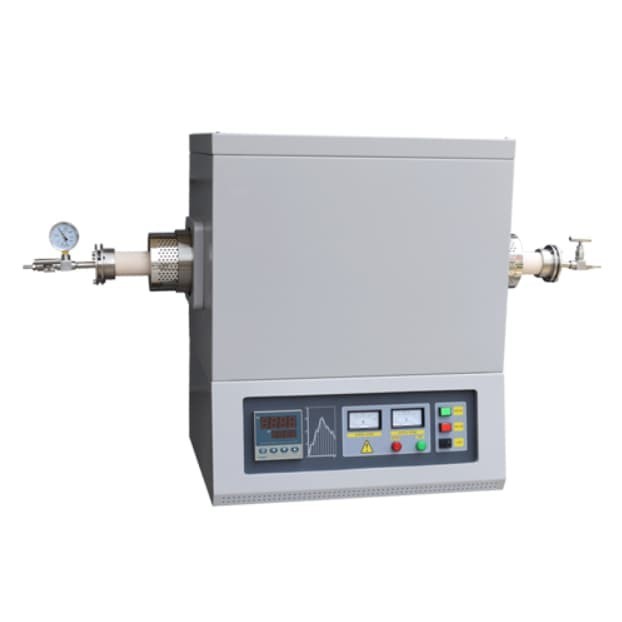
Custom tube furnaces offer unmatched versatility for diverse heating applications. Their design can be tailored to specific temperature ranges and materials, ensuring optimal performance for unique processes.
Precision is another significant advantage. These furnaces provide uniform heat distribution, which enhances the quality of your results. Whether you’re sintering ceramics or conducting metallurgical experiments, consistency is key.
Energy efficiency is also a notable benefit. Custom configurations often incorporate advanced insulation and heating technologies that minimize energy consumption while maximizing output.
Additionally, they promote safety in high-temperature environments. Many custom tube furnaces come equipped with advanced monitoring systems and fail-safes to prevent accidents during operation.
Their adaptability allows them to fit seamlessly into existing workflows. This means you can integrate them without overhauling your current setup or equipment extensively.
Applications and Industries that Use Custom Tube Furnaces
Custom tube furnaces find their niche across a diverse array of industries. In the semiconductor sector, they play a critical role in processing silicon wafers and other materials, ensuring precise temperature control for optimal results.
The ceramics industry also benefits from these furnaces. They are essential for sintering processes where uniform heating is paramount to achieving desired material properties.
In metallurgy, custom tube furnaces aid in heat treatment applications. They help enhance the mechanical properties of metals through controlled heating cycles.
Moreover, research laboratories utilize these systems for experimental purposes. Their adaptability allows scientists to conduct various experiments under specific atmospheric conditions.
Pharmaceutical companies rely on custom tube furnaces too. They facilitate drug formulation processes that demand exact thermal profiles to ensure product quality and safety.
Factors to Consider When Choosing a Custom Tube Furnace
Choosing the right custom tube furnace involves several key factors. First, consider the temperature range. Different materials require specific heating levels to achieve optimal results.
Next, think about the size of the furnace. It should accommodate your processes without wasting energy or space. A well-fitted furnace enhances efficiency and productivity.
Material compatibility is crucial as well. Ensure that the construction materials can withstand your intended applications without degrading over time.
Control features are another important aspect. Look for advanced monitoring systems that provide accurate temperature control and data logging capabilities.
Factor in safety features such as emergency shut-offs and insulation quality to protect both operators and equipment during use. Prioritizing these elements will help you select a tube furnace tailored to your needs.
Maintenance and Safety Tips for Operating a Custom Tube Furnace
Operating a custom tube furnace requires attention to both maintenance and safety protocols. Regularly inspect the heating elements for wear and tear. Any signs of damage should be addressed immediately to prevent malfunctions.
Ensure that all connections are secure, as loose wiring can lead to hazardous situations. Keep the surrounding area clean and free of flammable materials; this is crucial for safe operation.
Always wear appropriate personal protective equipment (PPE). Heat-resistant gloves, goggles, and lab coats provide vital protection when handling materials or adjusting components.
It’s also essential to familiarize yourself with the manufacturer’s guidelines. Each model may have specific requirements that need adherence for optimal performance.
Maintain a fire extinguisher nearby just in case an emergency arises. Being prepared enhances safety while working with high-temperature equipment like tube furnaces.
Conclusion: The Future of Precision Heating with Custom Tube Furnaces
The landscape of precision heating is evolving, and custom tube furnaces are at the forefront of this transformation. These versatile tools cater to specific needs across various industries, ensuring optimal performance and efficiency.
As technology advances, so do the capabilities of custom tube furnaces. Innovations such as improved insulation materials, enhanced temperature controls, and energy-efficient designs promise to make these systems even more effective. Industries from semiconductor manufacturing to research laboratories benefit from precise control over their heating processes.
Moreover, environmental considerations are becoming increasingly important. Custom tube furnaces can be designed with sustainability in mind, minimizing waste and optimizing energy use without compromising functionality.
Choosing a custom tube furnace means investing in quality and reliability. By understanding your unique requirements and keeping an eye on industry trends, you can select a system that not only meets current demands but also anticipates future challenges.
Precision heating solutions like custom tube furnaces represent a significant advancement for manufacturers and researchers alike. As we look ahead, it’s clear that these innovations will play a crucial role in shaping the future of many industries requiring advanced thermal processing techniques.